By Amanda Ombeva, SC4CCM Regional Technical Advisor
If you are working in supply chain, there have been probably been numerous times where you have been tempted to point a finger upwards, outwards, away to anyone else to say they are the problem. The central medical store, the district, the quantification task force anyone else but me is the reason why I always run out of products. The familiar denials often follow: they did not send me enough products; I don’t get what I ordered; there is not enough transport; when I went, they did not have any………..again it is all very familiar.
In the Rwandan districts of Ngoma, Rutsiro and Nyabihu, community health workers (CHWs) and health centre staff have been meeting together for the past nine months to take ownership for ensuring that resupply procedures are followed and there is a constant supply of products always on hand to serve the children within the communities. Recognizing the truth of the African proverb that as we point a finger outward, three fingers are always pointing back at us, these health workers have worked with the Ministry of Health Community Health Desk and the JSI-SC4CCM project to identify barriers in the supply chain at their level and a Quality Collaborative (QC) process to overcome these challenges.
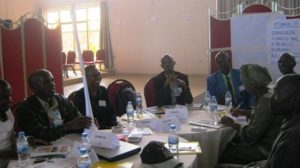
Inkingi imwe nti yubaka inzu – No man is an island
The health centre meetings consist of the CHW Supervisor, Pharmacy Manager, Data Manager and Cell Coordinators. The cell coordinators are the foot soldiers who go out to visit CHWs in the villages and make sure they are carrying sufficient products, maintaining stock cards, and ordering on time along with other supply chain tasks. The cell coordinators carry a supervision checklist then score and tally the results for CHWs within their cell. Once the score is tallied, all cell coordinators affiliated with the health centre come together with health centre staff to look through their combined data. As a group they go through a process of identifying the most common challenges faced by CHWs to ensure adequate supplies. At the health centre, they can then prioritize the issue to work on, drill down to the root cause of the current supply chain problem and then decide on an action plan to solve the problem or close the gap. Periodically, a coach from the district or central level will visit the team at the health centre to hear problems they are unable to resolve or to provide guidance on overcoming supply chain barriers. The collaborative part of this process occurs when different health centre teams meet at quarterly meetings to share lessons learned for implementing supply chain solution in various environments.
Skeptics (those finger-pointing folks referred to earlier) may argue that the supply chain is a linear process and those lowest down in the chain have the least ability to solve supply chain problems. The supply chain heroes in Rwanda feel otherwise: 87% of QC members now rate their knowledge of supply chain procedures at the community level following participation in the QC as “very good” or “outstanding,” and 80% of them now feel that they can carry out activities that result in a supply chain improvement in the community.
In describing the Quality Collaborative process, the supply chain heroes of Rwanda frequently say: “Umutwe umwe wifashisha Gusara ntiwifashya Gutekereza” or “Inkingi imwe nti yubaka inzu.” Both are local proverbs meaning “No man is an island.” By team work and local ownership, the Quality Improvement Teams have been able to find innovative ways to solve supply chain problems at the community level.